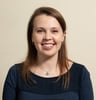
Kasha Dubaniewicz
Kasha is passionate about high-impact storytelling and believes in making positive changes that will lead to a better and happier world for all.
In the growing world, it feels like controlled environment agriculture (CEA) - and the ability to automate as many growing activities as possible – is all the rage. However, when growers are asked about the main factors that are holding them back from investing in automation, cost and complexity are usually cited as the major reasons, as well as the lack of credible data about the benefits.
It’s true that automation equipment within controlled agriculture requires hefty investment, which may not always seem worthwhile if you don’t know what sort of improvements you can expect after installing these at your growing site. That’s why we’ve done our own investigation, identifying four sources that show the real and measurable benefits of moving towards automation and regular data collection within controlled agriculture.
From a 50% increase in crop yield to saving over 700 input hours, take a look at the following four sources and their results. These are results experienced by real, working farms as well as extensive studies, and we hope that these success stories prove useful to you during your own journey in controlled agriculture.
For many experienced growers, the first step towards CEA usually involves the full or partial conversion of their longstanding open-field agriculture or soil-based operation to a controlled hydroponic system. But what kind of benefits can these growers expect to see – and how long will it take for these to take hold? Check out the following case study with Black Stump Farm, who has recently converted a third of their farm to hydroponics and seen immediate results.
Converting to controlled agriculture – a 50% increase in crop yield and eight-fold improvement in productivity
A berry farm in New Zealand recorded an impressive eight-fold improvement in its operation’s productivity, as well as a staggering 50% increase in crop yield within a single growing season. What’s even more noteworthy about these figures is that these are the results after only partially converting Black Stump Farm from traditional open-field agriculture to controlled growing in the form of hydroponics. About one third of the farm is automated by the Bluelab Pro Controller and Bluelab Guardian Monitor Connect, with owner and head grower, Nicky Kingsbeer, stating that their move to CEA has made her crops a far more viable option for the future. Read the full case study – and watch the video of Black Stump Farm – here.
The pH (potential Hydrogen) of your growing environment is one of the fundamental parameters of plant health – and for good reason! The pH determines if and how much of the nutrients you supply to your plants are available for uptake. This is why many CEA growers prioritise the automation of pH within their setup. But is it really such a big deal? This next piece of research tackles this question head on, determining the true cost of uncontrolled pH.
The true cost of uncontrolled pH – a 44% loss in tomato crop yield
Bluelab collaborated with the Center for Applied Horticultural Research for a report entitled ‘Effect of irrigation pH acidity and basicity on nutrient availability, plant health and yield of three plant species’. The three different plant species studied were tomatoes, petunias and three varieties of chrysanthemums. The report examined the results of plants grown within both acidic and alkaline pH ranges and compared these with plants grown within a pH range that wasn’t controlled. The results were unanimous across all plant species: all of these plants performed better and had better plant health at a consistent pH compared to uncontrolled pH. In fact, in tomatoes, there was an overall 44% loss in crop yield when the pH was left uncontrolled. Download the full report here.
For those growers who need to continue growing in soil, it may feel like many automation or monitoring activities are not worthwhile or relevant to you. This is why when we rolled out the Bluelab Pulse Meter beta testing project, we focused on discovering the real benefits of regular soil-based monitoring and data collection. Below, we look at the results seen by one participant, who started measuring noticeable differences within eight months.
The power of soil-based monitoring and data collection – a 10% increase in Grade A produce within 8 months
Southern Cross Horticulture is a New Zealand-based and family-owned operation that’s been growing and exporting kiwifruit for the past 40 years. Not only do they manage their own kiwifruit orchards and greenhouses, but Southern Cross also offers end-to-end orchard development as a service to growers and landowners. Rob St Leger, the former Greenhouse Nursery Technical Manager, used the Bluelab Pulse Meter for eight months as part of a beta testing project; Southern Cross was also a beta tester for the Bluelab Leap pH Probe. The business grows soil-based kiwifruit seedlings in their greenhouses, and it’s important that these seedlings are grown consistently in terms of their grade quality, as well as their overall plant health. They also used the data collected from their readings to monitor these factors over time. During those eight months of beta testing, the team at Southern Cross used the Pulse Meter to monitor EC, moisture and temperature, and noted a 10% increase in the overall number of Grade A kiwifruit plants they had at the end of that growing period.
For the vast majority of growers, taking the plunge from manual or hand nutrient dosing to fully automated nutrient dosing may seem like the ultimate automation investment you could make. Understandably, this is an area where growers need the benefits to be really clear to warrant sinking so much capital into one automation activity. One research report is showing promising results, where this investment has not only led to a reduction in input hours, but also large monetary savings over time.
From manual to automated nutrient dosing – save 700+ input hours and thousands of dollars
According to a report written by Grownetics, a move from hand dosing to automated nutrient dosing can result in a decrease in labour costs, as well as enormous savings in overall operational costs. This move to automated nutrient dosing not only saved a total of 758 input hours, but it also saved operational managers between US$11,362.50 to $568,125.00, depending on the size of their growing operation. The report looked at the potential savings for the following operation sizes: 10,000 square feet, 20,000 square feet, 50,000 square feet, 100,000 square feet, 250,000 square feet and 500,000 square feet. You can see a full copy of the report here.
Do you feel like your growing site could benefit from these types of improvements? If you’d like to speak to someone about automation and the requirements or concerns you have at your particular grow site, we’re offering free one-on-one personalised virtual consultations with our team of global experts.
Find out more and book your personalised consultation.
Submit a comment