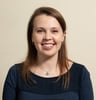
Kasha Dubaniewicz
Kasha is passionate about high-impact storytelling and believes in making positive changes that will lead to a better and happier world for all.
What does it really take to be successful in controlled environment agriculture (CEA)? Is it really just a case of maximising efficiency, optimising crop yield or boosting profits, or is there something more to the story?
In this article, we've reached out to top industry experts, who are all involved with CEA in some way, asking them about their insight into what really works, as well as where this growing method might be heading in the future.
What is CEA?
Before we jump into what the experts say about it, let's tackle what we mean when we refer to CEA. Put simply, CEA is a technology-based approach to growing, where one or more parameters are - as the name suggests - controlled in some way.
When we refer to automation, this refers to the process by which the control of parameters or variables becomes automatic through the use of tools and technology.
Quick links to the advice from each expert
- Know your crop data back to front: Chris Higgins, GM at Hort Americas
- Focus on increasing net revenue with automation: Andrew Clark, Lead Designer at WaterFarmers Urban Agriculture
- Aim for consistency and reduce water and fertiliser waste: Nick Cochran at Chinook Growers and Sunny Buds
- Hire the right talent and lean on your network to access shared knowledge: Matthew Mickens, Chief Science Officer at Elevate Farms
- Use continuous improvement in yield, flavour and quality to help your bottom line: Jeff Johnston, Manager at Grow + Gather
- Never gamble with plant health and crop yield: Doug Smith, Director of Cultivation Systems at Natura
Know your crop data back to front
Chris' personal history with CEA stretches back to 1996, when he first became involved with the commercial horticulture industry. In 2008, Chris, along with his business partners, founded Hort Americas, where he currently holds the role of President and General Manager. He is also the owner and founder of Urban Ag News.
For Chris, it's important to emphasise that nothing we're seeing in automation and CEA is, strictly speaking, anything new. Artificial lighting and glasshouses have been in use since the late 1800s/early 1900s. What is new, however, is the degree to which people are investing in technology, as well as the types of automation tools that are now available.
In the past, growers considered CEA and automation out of necessity, usually due to climate or geographical challenges; nowadays, automation technologies are being created to help facilitate business opportunities, both for the technology suppliers as well as the growers themselves. However, when money is driving the narrative, there are some pitfalls to keep in mind. One of the biggest challenges they're seeing at Hort Americas, Chris says, that while there are many top-of-the-range automation products out there, not all of these will work within a grower's existing greenhouse infrastructure. In addition, products from different brands may not necessarily be compatible.
There's no denying that automation can be beneficial. It can help growers better manage their labour costs and resources (especially water), and may also improve crop yield. However, as Chris points out, a greenhouse's automation technology is only as good as its operator.
That's why, whenever he speaks to a start-up CEA grower, he'd advise against investing too much, too soon. Instead, he'd encourage them to invest in their site's buffer capacity, making improvements so that their system is better able to handle extremes and fluctuations.
The one thing that he does advise is investing in sensors that allow growers to capture the nine variables that are going to help them be successful in crop management: water, root-zone temperature, light, humidity, environmental temperature, wind, carbon dioxide, nutrients and oxygen.
Where to invest as a grower new to automation
When it does come time to invest in automation, the grower should identify their main reasons for doing so. Is it about freeing up time during their day? Is it about producing better quality? Is it about making their workforce more efficient? Determining the reason as to why they're investing will help them find a tool that's best suited to their skillset and goals, which means that they're more likely to succeed.
Not only that, but the grower needs to get well acquainted with their crop data. This will help them determine which of the nine variables are impacting or limiting them the most; this should never be done from their gut, but always from their data. This means that they'll be investing in a solution that truly helps them solve the problem that's unique to their grow site.
In Chris' eyes, it's this knowledge of site data that seems to be the mark of a successful CEA grower. Once the grower knows their business back to front, they'll know exactly what they need to start working on or troubleshooting as soon as a problem comes up.
Helpful links
- Find Chris Higgins on LinkedIn
- Read more about where to invest when it comes to hydroponic technology on UrbanAg News
- Watch Hort America's Mastering Controlled Environment Technology video series for more on successful CEA
Focus on increasing net revenue with automation
Andrew Clark is the Lead Designer for WaterFarmers Urban Agriculture, a Canadian design-build firm specialising in CEA and ecological landscaping located in Southern Ontario. Andrew's personal background lies in mechanical engineering, and his journey with automation began out of simple necessity. That's because more and more of his customers needed to be able to constantly control and monitor pH and EC.
Since 2017, the team at WaterFarmers Urban Agriculture has been supporting growers and new farms. Their clients grow a wide range of crops and at a variety of site types - from leafy greens to tomatoes to mushrooms, using indoor facilities, shipping containers, greenhouses or outdoor plots.
For Andrew, there are three benefits of automation that immediately come to mind. These include reduced manual labour, the fact that automation technology runs around the clock, as well as the ability to have remote access to your parameters through the use of alerts.
The important role of automated dosing
While automated pH and EC dosing systems based on sensor feedback are important for all indoor growing operations, they're essential for recirculating systems. With this type of system, it's imperative to have automated dosing to ensure that water returns to appropriate levels after irrigation events or during top-off. The alternative would be constant attention from on-site employees, as dosing based on ratio to flow isn’t an option since nutrients would build up over time.
While Andrew acknowledges that automation can increase the efficiency of a CEA site, which could also bring increased yields and profits, there's no denying that a focus on automation has some potential negatives. This focus could give rise to a situation where a CEA business procures equipment that is too complicated for their needs, and they spend too much time getting it commissioned, optimised and training employees to operate it. This could, inadvertently, remove the focus from what actually makes the business money - selling food.
And that's the important thing to note: automation in and of itself doesn’t guarantee increased efficiency or profits; the technology needs to be on a scale that suits your farm and your business model.
After all, CEA automation technology is expensive, especially when compared with outdoor or simple hoop house growing. Even comparing traditional greenhouses with supplemental lighting to completely indoor CEA, the square foot costs are often double or more. From the perspective of many small outdoor and greenhouse farmers, the money spent on automation is not proportional to the benefit, which should be increased net revenue.
That said, there is immediate value when a piece of technology can automate a simple repetitive task, such as turning lights on and off, adjusting a thermostat, dosing acid into an irrigation tank or opening an irrigation valve on a timer. For existing farms, Andrew always recommends first investing in a simple piece of automation that will allow growers to spend more time on growing food.
Lastly, in terms of what makes a CEA grower successful, Andrew names two stand-out factors: well-developed standard operating procedures and record keeping.
Helpful links
Aim for consistency and reduce water and fertiliser waste
Nick Cochran has been involved in the business of growing from way back; in fact, when he was growing up, he remembers growing fruit and vegetables to sell at his local farmers' market. In 1999, he started growing cannabis hydroponically and, in 2012, when medicinal cannabis became legalised in Washington State, he made his way back to this industry. Nowadays, he works with partners and grow teams across a number of sites, where they grow cannabis primarily outdoors, as well as in CEA greenhouses.
Nick's automation journey began in 2015, when the expansion of his grow sites necessitated the move to using automatic watering systems via the use of drippers. These watering systems ensured that his plants would always be watered, while freeing up his time to focus on his overall crop and site performance. In 2017, he purchased his first Bluelab pH Controller, which he installed in a room reserved for research and development. The results he saw with that first crop were impressive, which helped inform Nick's future automation investments. For his particular growing needs, he knew that controlling pH - and therefore keeping this parameter at consistent levels - would be a big priority.
The secret to consistent crops is system stability
When it comes to the three biggest benefits that he's experienced by choosing to automate, he lists saving on time as well as labour costs, the above-mentioned ability to maintain stable pH and EC, which has led to more consistent crops as well as less fertiliser waste, and water conservation, as his automated watering systems ensure they only use what they need.
Automation also has practical benefits for any growers who are running and managing several different grow sites at multiple locations. Automating pH and EC, as well as watering, has ensured that Nick and his partners always know that these sites are always operating consistently, even though these sites all have different water sources.
This consistency plays a huge role in their overall crop yield. If he and his grow teams were forced to do all of these now-automated activities by hand, they would simply not be able to grow as much, nor would they be able to guarantee their crop quality.
Automation technology may seem expensive, especially when considering the upfront costs, but, for Nick, the time and money (including labour costs) you could potentially save - as well as being able to produce more consistent quality and volume - outweigh this particular negative.
Nick names the two factors that have contributed to his success as a CEA grower: consistency and training. He trains two people at each farm to ensure that proper standard operating procedures are followed, and also hosts weekly meetings so that they can address and solve any issues when these come up.
Helpful links
- A case study on keeping a step ahead in a competitive and ever-changing medicinal cannabis industry
- Read about the company dedicated to medicinal cannabis product development and research
Hire the right talent and lean on your network to access shared knowledge
Whether you're growing plants in space or on Earth, it turns out that there happens to be an overlap when it comes to the benefits of automation within both these environments.
This is what Matthew Mickens, the Chief Science Officer at Elevate Farms, discovered during his three years at NASA's Kennedy Space Center, where he completed his postdoctoral fellowship. While Matthew doesn't consider himself to be a traditional grower, instead he's come into the controlled agriculture space as a plant scientist and researcher, where he used his time at NASA to research plant response to various light wavelengths.
The knowledge he acquired at NASA ties neatly into his role at Elevate Farms, a business that leans on 30 years of research into factors like customised light recipes so that they can deliver optimal produce to their customers. By creating state-of-the-art vertical farming facilities, Elevate Farms relies on their chosen technology partners and systems to ensure that they're growing consistently high-quality leafy greens across all their sites.
Applying knowledge from NASA to support CEA initiatives in the community
One of Matthew's current key tasks is to oversee the installation of a large indoor farm based in New Jersey, but he also advises and assists with operations at Elevate Farms' other vertical farming facilities. It's this interaction with large indoor facilities that helped Matthew spot the similarity with the problems they were trying to solve at NASA. Whether it's a crew of astronauts growing leafy greens in space or a team running a large CEA site on Earth, automation helps to save both in terms of labour and time.
And Matthew has also seen the many other benefits of the multiple automation systems they have in play at Elevate Farms' sites. While he holds that their customisable lighting systems are the technologies that make the single-biggest impact on their overall crop yield, he also acknowledges that pH and EC control, as well as the automation of their fertigation system, have ensured that their plants are consistently getting what they need. In fact, when it comes to what a CEA grower should consider automating first, Matthew is quick to mention fertigation.
That said, Matthew emphasises that the talent you hire at an indoor farm is just as important as the automation technology you decide to invest in. After all, these technologies require the right operators who are able to understand the systems and spot issues early on; without this ability, it's all for nothing.
This becomes even more apparent when you consider that automation often requires hefty monetary investment. However, with the right technology - and the right talent driving these systems - these upfront costs are quickly balanced and then eventually surpassed over time.
This is where Elevate Farms finds itself now where they're able to differentiate themselves from other vertical farming facilities, who normally target high-end sellers for their produce. Instead, Elevate Farms bases its facilities in high-density urban centres, providing affordable yet high-quality produce to the communities in the immediate area. This ability to improve accessibility while cutting down on transportation impact, along with the traditional vertical farming benefits of using 90% less water and space, allows Elevate Farms to place sustainability and social responsibility at the centre of their mission statement.
Lastly, when it comes to what makes a CEA grower truly successful, Matthew identifies an aspect that has helped him significantly across his own career: networking. As he puts it, the CEA community is really tightknit, and staying as connected as possible ensures that you have access to the knowledge, skills and talent you'll need to succeed at your CEA grow site.
Helpful links
- Find Matt on LinkedIn
- Follow Elevate Farms on Twitter
- Watch Bluelab's webinar with Matt, where we discuss how to grow more food with less resources. Now on-demand.
Continuous improvement in yield, flavour and quality will help your bottom line
Jeff Johnston first came into the world of growing after building a 30-year career as a real estate developer. Swapping real estate for plant produce, he now manages the ground-breaking Grow + Gather site with his business partner George Gastis. Officially launched in December 2019, Grow + Gather is a bustling community hub, where an old auto station in Englewood, Colorado, has been converted into a food market, cafe, restaurant, as well as a number of different growing areas.
With Grow + Gather, Jeff says that their overall goal is to bring food production far closer to the people consuming those products. This has resulted in the creation of their urban gardens, a rooftop greenhouse as well as their innovative hydroponic farm; everything grown here goes straight to the on-site market, as well as the kitchens of their coffee shop and full-service restaurant, the Feedery. With this unique model, they've gone on to cement their status as a successful self-sustaining system within a high-density urban centre.
For Jeff, part of this success can be attributed to their decision to automate within their growing areas from early on. By choosing to be based within a busy urban centre, they needed to offset their expensive real estate costs by cutting down on labour - and it's automation that allowed them to do just that. Once the automation systems were up and running, Jeff took the time to truly understand the technology and trust this to operate correctly; over time, he was able to reduce the amount of people required to manage the growing areas at Grow + Gather.
In fact, during the worst of the turbulent COVID-19 period, Jeff was able to operate the hydroponic farm by himself. If it wasn't for automation, he acknowledges that this wouldn't be possible, as he'd need to spend many more hours on checking sensors and doing manual dosing.
Tweak water flow and nutrient mixes to improve yield and quality
Apart from helping to reduce labour costs, automation has also helped them achieve what Jeff describes as an incredibly consistent crop with a predictable yield. As soon as their automation systems were installed, Jeff noted impressive results, where their normal crop yield was almost tripled straight away. At Grow + Gather, they largely focus on growing leafy greens, where their 1,200-square-foot hydroponic room, which makes use of a cutting-edge two-channel hydroponic system, is currently able to produce the same yield as 2.5 acres of traditional open-field agriculture in Colorado.
Instead of having to worry about 15 different variables, automation within their CEA site allows Jeff and his team to focus on what really matters: optimisation and experimentation. Since Jeff knows that his important parameters like pH and EC are taken care of, he can spend his time tweaking variables like water flow and nutrient mixes to further improve yield and quality.
When it comes to what extent CEA growers need to automate, Jeff says that, for his needs, he has an all-or-nothing approach. That's because, if he only had one automation system in place, he'd only be controlling one variable, which is a small part of the overall picture and would therefore not help him in his biggest priority - to cut down on labour.
While he recognises that there are barriers to CEA and automation, such as upfront costs and upskilling to learn and operate the equipment, his own experience testifies to the dramatic benefits that automation brings with time.
Ultimately, what's helped Jeff and the team at Grow + Gather progress so quickly within CEA has been the lack of expectations of what growing should be like. As Jeff puts it, if he had been trying to do this after a 20-year career growing plants in soil, then it would be a completely different story. Instead, he has come into the Grow + Gather venture wholeheartedly committed to this new way of growing, which he likens as being closer to manufacturing than traditional farming. Automation has allowed him to streamline their operation, where they're able to grow produce every single day of the year while having the freedom to continuously improve factors like yield, flavour and quality.
Helpful links
- Follow Grow + Gather on Facebook to follow their growing journey
- Watch how Black Stump Farms increased yield by 50% with automation
- How to monitor your fundamental parameters: pH, EC and temperature
Never gamble with plant health and crop yield
Although Doug took a 20-year hiatus from his long-held passion for plant propagation, automation has been part of his daily life for decades. During his 17-year career in the USAF, automation played a pivotal role as he moved from in-flight refueler to pilot on both Air Force and civilian air crafts.
It was during this time in the Air Force that he first learned that the true value of automation systems comes from the complete trust that you’re able to instill in them. These same lessons applied when he left the Air Force and started designing water automation systems for the municipal water industry, eventually joining forces with Natura as their Director of Cultivation Systems.
Natura prides itself on its California-based state-of-the-art facility that houses everything needed to successfully launch and scale cannabis brands. Their 200,000-square-foot grow facility contains cutting-edge technology, including automation systems, that allows cannabis brands to produce high-quality products, and predictable crop yields all under one roof.
Automation also plays an important role in his personal life. Doug has a personal research project that extends beyond his work at Natura, where he makes use of aquaponic methods in both indoor and outdoor closed-loop systems, in an attempt to break the barrier of what biological organics are able to do.
The 3 big benefits of getting CEA right
When it comes to the biggest benefits of choosing to grow plants using automation, he cites three: The standardization of irrigation and nutrient requirements (and therefore the reduction of variables you need to manually manage), the ability to capture and analyze data, as well as daily schedule control.
In fact, what CEA growers should be attempting to achieve with their grow site is to recreate the best possible environment for plant development, mimicking the pinnacle of what can be found in nature. This can be achieved through the thorough analysis of your plants’ uptake biology, as well as ensuring that you’re creating a customizable climate environment. Making sure that both these processes can be automated going forward is imperative.
While Doug recognizes that there are significant barriers to automation, he believes that the best results come from choosing the right equipment, and then learning to master and control that equipment to ensure that you can meet all your variable requirements. When asked about what makes a CEA grower truly successful, he views this through the lens of the automation specialist that he is: First, to never stop evolving, and secondly, to make sure that you keep customizing your automation applications.
Ultimately, Doug doesn’t think growers should gamble when it comes to plant health and crop yields. By choosing to automate early on in the growing process, growers are being proactive about getting consistent results with their crops. Doug knows that this is something that cannot be achieved without automation.
Helpful links
- How one grower started a successful commercially viable passionfruit farm with no experience
- Follow Natura on Instagram, Facebook an LinkedIn
What are the real, measurable benefits of moving to automation in controlled agriculture?
Now that we've heard from our experts, you may be curious about seeing the hard numbers when it comes to choosing to take the plunge with automation investment.
In our article on 'What are the real, measurable benefits of moving to automation in controlled agriculture?', we look at the real results experienced both by growers as well as thorough research projects examining factors like controlled versus uncontrolled pH and overall operational savings.
If you want to learn more about the future of controlled environmental agriculture, watch our webinar series dedicated to asking the tough questions about CEA. We ask industry experts questions about sustainability, diversification and growing more food with less resources.
Watch the FOCEA webinar on-demand here.
What questions do you have about being successful in CEA? Let us know in the comments below, and we'll get back to you.
Submit a comment